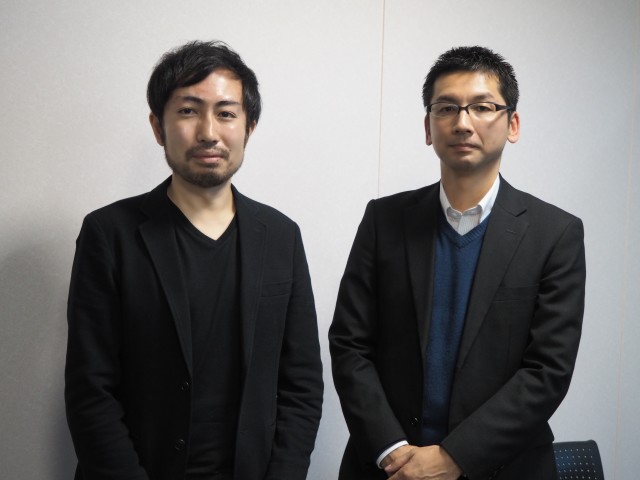
『マイクロコミューター豊島屋モデル』をご存じだろうか?これは、3Dプリンターを使って製作された1人乗り用の超小型EV(電気自動車)だ。
製作したのは、自動車メーカーの本田技研工業株式会社(以下、ホンダ)と、デジタル技術を駆使した新しいもの作りサービスを提供するスタートアップ企業の株式会社Kabuku(以下、カブク)。 神奈川県鎌倉市のお菓子メーカー、『鳩サブレ』で有名な豊島屋向けに、配送サービスをおこなうための車両として製作されたものだ。
2016年10月に開催されたイノベーション系展示会「CEATEC JAPAN 2016」に出展され話題を呼んだので、クルマ好きやEVに興味がある読者なら覚えている方も多いだろう。
新しい“クルマづくり”を予感させるこのEVについて、製作に携わったホンダ スマートコミュニティ企画室・主任の榊 秀雄氏と、カブクでインダストリアル デザイナーを務める横井康秀氏にお話をうかがった(全2回)。
|
|
ホンダ『MC-β』をベースに製作
──まず、『マイクロコミューター豊島屋モデル(以下、豊島屋モデル)』は、どんなクルマなのかについて教えて下さい。
榊:フレームやモーターなどのパワーユニット、ドアや内装などは弊社が開発した(写真下の)『MC-β』(注1)がベースになっています。乗車定員は2人乗りから1人乗りに変更していますが、ボディサイズやモーター出力、バッテリータイプなど、主要諸元(注2)はほぼ同じです。 これをベースに、「カブク」さんが外装カバーや荷室などを3Dプリンターで製作され、最終的に組み立てました。
オープンイノベーションの一環として共同開発
──どのような経緯で製作に至ったのでしょうか?
榊:2013年から実証実験を行っている『MC-β』は、おかげさまで各方面から様々な反響を頂いております。それらの中のひとつとして、「豊島屋さんで鎌倉の細い道を走れる配送用車両として使いたい」とのお話をいただきました。
今まで『MC-β』の実証実験でも、自治体様と共同で業務用途などを検討してきました(注2)。今回の「豊島屋モデル」は、企業様などからの個別のニーズに合わせたカスタマイズモデルという新たな試みといえます。
|
|
そこで、弊社が現在進めているオープンイノベーションの一環として、以前から展示会などでお知り合いになっていたカブクさんと共同で開発させて頂いたというのが大まかな流れです。
──外装カバーはABS樹脂を3──装カバーなどは具体的にどのように製作されたのでしょうか?
横井:弊社(カブク)がご提供しています『Rinkak マスカスタマイズ ソリューション』をご提供させて頂きました。これは、自動車や家電など、従来ではカスタマイズできなかったモノを、1点モノとしてカスタマイズし、カブクがネットワークしている世界30カ国以上の産業用3Dプリント工場を繫いで、工場の遊休期間などに製品を作ってもらうサービスです。
従来の金型や材質を切削して製造する方式と比べると、3Dデータさえあればどこででも生産できるのがメリットです。また、金型などを作る時間が不要なため、短期間で製品を作ることができます。
|
|
今回、具的には豊島屋さんのご要望をお聞きしてデザインを3Dデータで作成し、それを依頼した工場に送り作ってもらいました。
──使った材質は何でしょうか?
横井:ABS樹脂です。家庭用3Dプリンターで使われているようなものではなく、工業用3Dプリンター用の材質を使用しています。剛性や強度などは、クルマのバンパーなどに使われていものと遜色ないですね。
榊:外観カバーに樹脂を採用することによって、デザインの自由度が上がっています。
一般的なクルマでは、モノコックフレームを採用しますが、その場合は外装にもある程度強度が必要になります。
でも、それでは外観デザイン変更の難易度が高くなってしまう。今回ベースとしているMC-βは、パイプフレーム構造を採用しています。外装カバーの強度などを比較的気にしなくていいため、デザインの自由度が上がります。
2輪車のスクーターのような構造をイメージして頂けると分かりやすいと思います。
3Dプリンターの高い精度を実証
──実際に3Dプリンターで製作してみて大変でしたか?
横井:これだけ大きなものを作るのは、私自身も、業界にとってもほとんど先例がありませんでした。なので、今だから言いますが、出来上がるまではドキドキしていました(笑)。 今回は、ベース車両があり外装カバーの取り付け位置などが決まっていたので、(3Dプリンターに入力する)データを作成する際にそういった情報もいれています。ですが、実際に上がったものに歪みなどがあると、ちゃんと取り付けできない可能性もありました。何分、初めて作る大きさだったのでやってみないと分からなかったんです。もし、一発で付かない場合は、再設計や再生産が必要な場合も覚悟してました。
榊:実際に製品が出来上がって取り付けてみると、なんの問題もなくピッタリと付いたんです。正直これには驚きましたね。3Dプリンターの精度はかなり高いということが分かりました。
横井:ほっとしました(笑)。「CEATEC JAPAN 2016」への出展が決まっていたので、やり直しをするとなると、かなり時間的にきびしかったので。 今回は、複数の国内工場で製作して頂いたのですが、いずれも最高級の3Dプリンターを導入している工場にお願いしました。高い精度を出すには、やはり3Dプリンターもいいものを使う必要がありますね。
デザインの自由度や製作期間の短縮がメリット
──3Dプリンターを使うメリットは何でしょう?
横井:まず、先程もお話した通り、金型などが不要なため製作期間が短くできますね。今回、デザインから設計、そして3Dプリントして完成までにかかったのは約2か月です。
金型で作る場合は、金型業者さんと折衝し、ちゃんとした金型ができるまでに何度か修正したりするのが普通ですから、そんな短期間ではできません。また、金型自体を作るコストも抑えられます。
あと、デザイン的にも3Dプリンターにしかできないものもあります。
今回の場合では、車体側面などに入れた豊島屋さんのエンブレム(上)がいい例です。幾重もの筋が見えると思いますが、これは、積層跡といって3Dプリンターで製作した場合に出るものです。通常この筋は磨いて落とすのですが、「年輪のように見える」ため、歴史がある鎌倉や豊島屋さんのイメージに合うと思いあえて残しました。
車体後部にある、何羽もの鳩が重なったデザインも、3Dプリンターならではですね。これらは金型でも不可能ではないかもしれませんが、作るとなるとかなり熟練の技術と時間が必要になるでしょう。その点、3Dプリンターならデータさえあれば簡単に作れてしまうのです。
短い時間で、デザインも自在に作れる3Dプリンター。次回は、この「豊島屋モデル」により、今後クルマづくりがどう変わるのかについて、お二人に語ってもらう。 (文中敬称略)
*注1:以前FUTURUSでも紹介した『MC-β(エムシーベータ)』は、ホンダが開発したスマートモビリティ。走行時のC02排出量ゼロの小型EVだ。軽自動車と原付4輪車の間に位置する新カテゴリーの乗り物として、国土交通省が検討している「超小型モビリティ」の規格に合わせて製作したもの。この規格のクルマは現在、国土交通省に申請を出して承認された自治体のエリアのみで走行が可能だ。
*注2:ホンダでは、2013年から熊本県(観光や業務利用)、さいたま市(カーシェアリングや子育て支援)、宮古島市(再生可能エネルギー活用や外部給電)などで実証実験を実施している(詳細は<【未来予想図2020】ホンダが考える「スマートモビリティ」、クルマだけでなくエネルギーも作る>参照)。
*注3:『MC-β』主要諸元 ■全長×全幅×全高:2,495×1,280×1,545(各mm)■最高速度:70km/h以上■モーター出力:定格6KW/最大11KW■バッテリー:リチウムイオンバッテリー■最大航続走行距離:80km以上■充電時間:3時間以下(200V)、7時間以下(100V)
【取材協力】
本田技研工業株式会社
株式会社カブク